Electrical Compliance
and Management
At Phoenix Compliancy Management our highly trained and experienced consultants provide expert advice and independent consultancy to comply with IET Wiring Regulations. We pride ourselves on providing a bespoke and personal service to our clients, as we are independent our clients are assured of totally impartial advice and reporting.
We carry out audit inspections relating to the service, maintenance and installation of your Landlord owned equipment, ensuring that all service, remedial and installation works have been completed in a safe manner and in accordance with the relevant industry regulations and manufacturers' guidance.
Please find detailed below a list of our services:
- On site quality control inspections of domestic and communal EICR's, EIC's and MWC's.
- Desk top auditing of EICR and EIC.
- Emergency lighting servicing onsite quality control inspection.
- Emergency lighting asset register.
- Design, Specify and procurement of all projects.
- Project management Decent homes.
- 30 year plan rising and lateral mains.
- Audit of the associations electrical policies, procedures and supporting electrical management processes.
- Production of Electrical policies.
- Production of Electrical specifications.
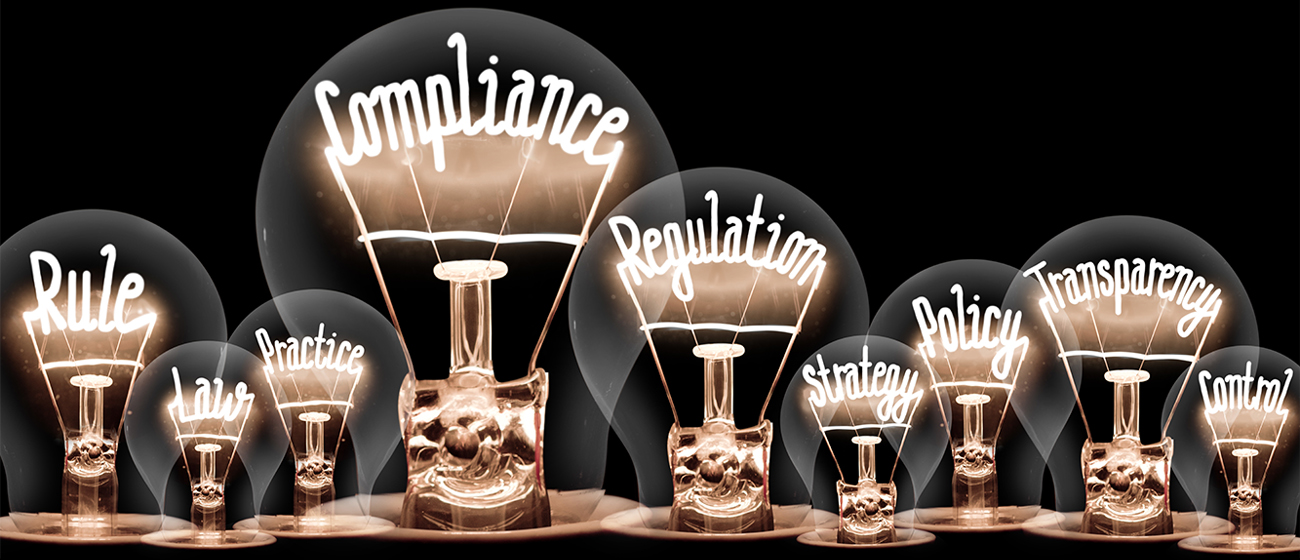
*EICR - Electrical Installation Condition Report. EIC - Electrical Installation Certificate. MWC - Minor Works Certificate
Our Risk Management Services Cover:
Quality Control Inspections
Our onsite quality control inspections reports will detail the installation visited by our inspector and findings, including inspections carried out in accordance with the BS:7671, relevant industry regulations and manufacturers' guidance. Our reports detail the compliance of the service using photographs by way of evidence and can be used for when the contractor reports completion and any remedial works claimed for.
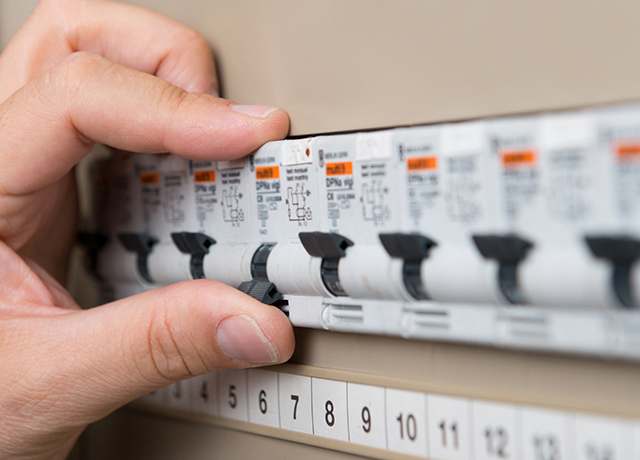
Management System Audits
A compliance audit is a detailed review of the current policy, management plan, control procedures and day-to-day activities to determine whether current control is compliant with current legislation, guidance and it is effective. Our audits identify whether precautionary measures remain effective, the current condition and performance of the system, management systems in place and identify arrangements for control parameters and that monitoring is completed by a competent contractor.
Our in-house specialist consultants work with our clients to assist with the tender documentation, design process and management of the project. We will manage the project with a systematic process to ensure the contractor is performing to the expected standards, regulations, CDM duties and best practise. We will provide weekly progress reports with photographic evidence, valuation reports, payment certificates and completion certificates to assist with the management of the project.
Emergency Lighting
Our onsite quality control inspection reports will detail the installation visited by our inspector and findings, including inspections carried out in accordance with the client's specification, relevant industry regulations and manufacturers' guidance. Our reports detail the compliance of the service using photographs by way of evidence and can be used for when the contractor reports completion and any remedial works claimed for.
Emergency Lighting Asset Register
With large stocks and inaccurate asset registers we are able to assist the client with a detailed asset register for their schemes accompanied by a report on the health of the system and a layout of the scheme.
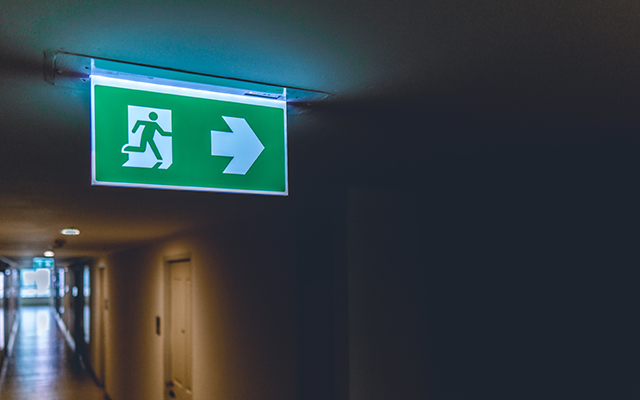
How Can We Help
Our specialist consultants assist the responsible person on a range of control issues and risk management to comply with statutory requirements, including project management.
Visit our contact page for more information or fill out the contact form at the bottom of this page and we will get back to you as soon as we can.
Dutyholders & Landlords Responsibilities for Electrical Installations
Why do we have to carry out an Electrical Installation Condition Report every 5 years?
Table 3.2 of Guidance Note 3 Inspection & Testing sets out the suggested initial frequency for the various routine checks on electrical installations. It gives suggested starting intervals for a duty holder to consider when implementing a maintenance plan for an installation. It must be remembered that "routine checks" and "periodic inspection and testing" by a competent inspector are only a part of the requirement for maintenance and the duty holder has a continuing on-going responsibility for the safety of an installation.
Note: Duty holders are reminded of the requirements of Regulation 4(2) of the electricity at work regulations 1989 - undertaking routine inspection and testing of their installations will assist in meeting this duty.
5.jpg)
Table 3.2
Type of installation | Maximum period between inspections and testing (note 8) | Notes |
Domestic accommodation - rented houses and flats | Change of occupancy/5 years | 1, 2, 10 |
Rented accommodation (Houses of Multiple Occupation - halls of residence, nurses' accommodation etc. | Change of occupancy/5 years | 1, 2, 10, 11 |
Table 3.2 Notes:
- Note 1 Particular attention must be taken to comply with SI2002 No. 2665 - Electricity Safety, Quality and Continuity Regulations 2002 (as amended).
- Note 2 Electricity at work regulations 1989, Regulation 4 and Memorandum of guidance (HSR25) published by the HSE.
- Note 8 The person carrying out subsequent inspections may recommend that the interval between future inspections be increased or decreased as a result of their findings of their inspection.
- Note 10 The landlord and tenant act 1985 requires that properties under the act have their services maintained. Periodic inspection and testing are the IET recognised method of demonstrating this.
- Note 11 The management of houses in multiple occupation (England) Regulations and the management of houses in multiple occupation (Wales) Regulations.
The suggested initial frequencies for inspection and testing given in Table 3.2 are recommendations and not legal requirements. It is the duty holder's responsibility to determine when the next periodic inspection is undertaken.
Regulation 114 Relationship with Statutory Regulations BS7671:2018 states the following:
The regulations are non-statutory. They may, however, be used in a court of law in evidence to claim compliance with a statutory requirement. The relevant statutory provisions are listed in Appendix 2 (BS:7671) and include Acts of parliament and regulations made thereunder. In some cases, statutory regulations may be accompanied by Codes of Practice approved under section 16 of the Health and Safety at Work etc. Act 1974. The legal status of these Codes is explained in Section 17 of the 1974 Act.
What are C1, C2, C3 and FI observations on an Electrical installation Condition Report?
The Electrical installation Condition Report should identify any damage, deterioration, defects and conditions within the installation that give rise, or potentially give rise, to danger. Each observation should be written in a clear, accurate and concise manner that is likely to be understood by the person ordering the work. Technical terms should be avoided or explained unless it is known that the recipient is an electrical engineer or electrician.
An Electrical Installation Condition Report is intended to be a factual report on the condition of an installation, not a proposal for remedial work. Therefore, each recorded observation should describe a specific defect, omission or item for which improvement is recommended. Each observation relating to a concern about the safety of the installation should be attributed an appropriate Classification Code selected from the standard codes C1, C2, C3 and FI. Each code has a particular meaning:
- C1 - 'Danger present'. Risk of injury. Immediate remedial action required.
- C2 - 'Potentially dangerous'. Urgent remedial action required
- C3 - 'Improvement recommended'.
- FI - 'Further investigation required'
If any observation in the report has been given a Code C1 or Code C2 classification, or if any observations require further investigation to determine whether danger or potential danger exists, the overall assessment of the condition of the installation must be reported to be 'unsatisfactory'. If there are no observations in the report classified as C1, C2 or FI, it would not be reasonable to report the overall condition of the installation as unsatisfactory.