Passenger Lifts and Mobility Equipment
Our inhouse specialist lift consultants provide expert advice and independent consultancy on a comprehensive range of passenger lifts and mobility equipment, service/maintenance audits and advice, management system audits, stock condition surveys and project management to assist you in complying with the statutory requirements.
Dutyholders and Landlords Responsibilities for Lifting Equipment and Operations
The Lifting Operations and Lifting Equipment Regulations (LOLER) and The Provision and Use of Work Equipment Regulations (PUWER) are in place to ensure that all lifting equipment is used in a safe manner. Any organisation whose employees use or operate lifting equipment in the workplace required to comply to these regulations, which come under the Health and Safety at Work Act.
These regulations require all lifting equipment to be appropriately managed by a competent person to ensure safety for users. The regulations require that all lifting equipment is to be examined on a regular basis by a qualified person to ensure that all equipment is fit for purpose and safe for users. It is the responsibility of the dutyholder or landlord to make sure the examinations are carried out and that all records of each examination are kept and suitably filed. The identified sections of equipment must then be suitably marked with any defects being reported to the responsible person(s).
Our Risk Management Services Cover:
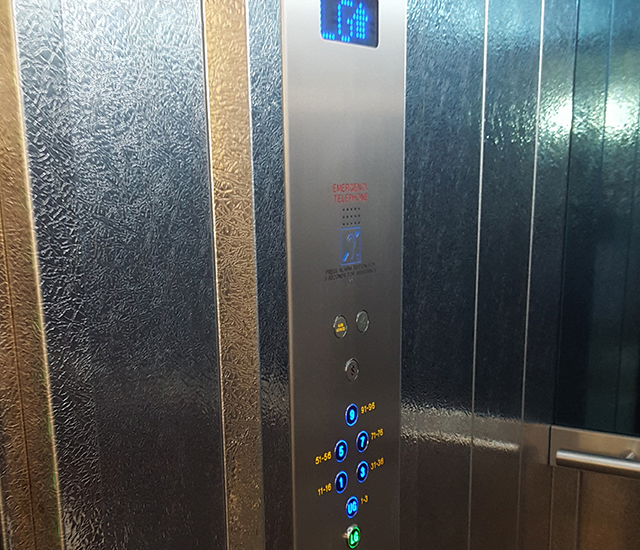
Stock Condition Surveys
Our bespoke surveys review the associated equipment, design, performance, life expectancy and condition. We provide a professional report to advise on whether the equipment is fitted to current standards, health and safety risks precautionary measures are implemented, and areas of non-compliance in accordance with the current regulations and standards are adhered to.
Service/Maintenance Audits and Trusted Advisory
Our independent audit reports will detail the property visited by an inspector and findings, including inspections carried out in accordance with the Lifts Regulations 2016, British Standards and best practice. Our reports detail the compliance of the service using photographs by way of evidence and can be used for when the contractor reports completion of remedial works.
Reports will additionally detail other issues identified, such as security matters, water leaks, and damage/vandalism at the property. In addition, we can monitor and advise on LOLER inspection certificates and works outside of the maintenance specification, checking value for money on contractor referrals.
Management and Operational System Audits
Our management system audits are a detailed review of the management plan, safety precautions, project development and contractor competence to determine whether current management is effective, and works are carried out in accordance with the relevant regulations and standards. Our audits identify whether precautionary measures remain effective, the current condition and performance of the system, management systems in place and projects are completed in accordance with the deadline date.
Contractor Referrals
Our in-house technical consultants provide trusted advice for lift repair, upgrade or refurbishment referrals recommended by contractor. Ensuring that the lift is appropriately repaired, upgraded or replaced will save our client unnecessary expenditure on assets that are still fit for purpose and provide the resident/customer a reliable lift service. By evaluating spares availability, breakdown history and beyond economical repair requiring refurbishment; we can advise on options for repair, upgrade and refurbishment in line with the client budgets and requirements.
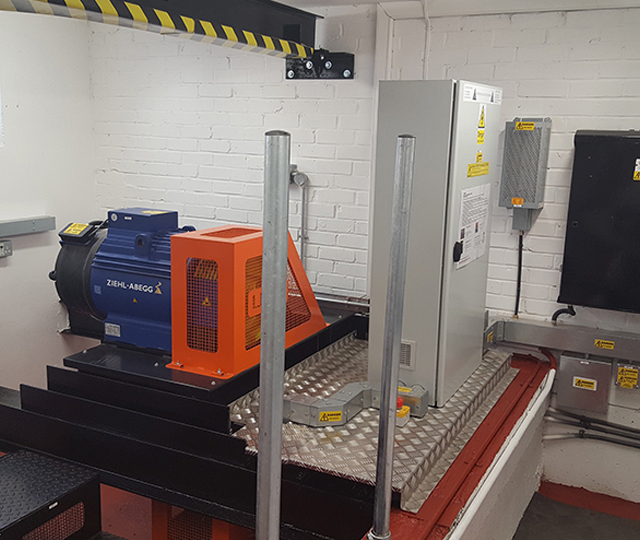
Bespoke Specification Production
Our qualified project consultants provide bespoke service, maintenance, refurbishment and new installations specifications based on individual client requirements, industry best practice, statutory obligations and supplementary testing requirements. We assist with the mobilisation of the specification to ensure adherence, which can be monitored ongoing with our independent auditing.
Refurbishments, Replacements and New Developments
Our specialist consultants work with our clients and assist with the tender documentation, design process and management of the project. We will manage the project with a systematic process to ensure the contractor is performing to the expected standards, regulations, CDM duties and best practise. We will provide weekly progress reports with photographic evidence, valuation reports, payment certificates and completion certificates to assist with the management of the project.
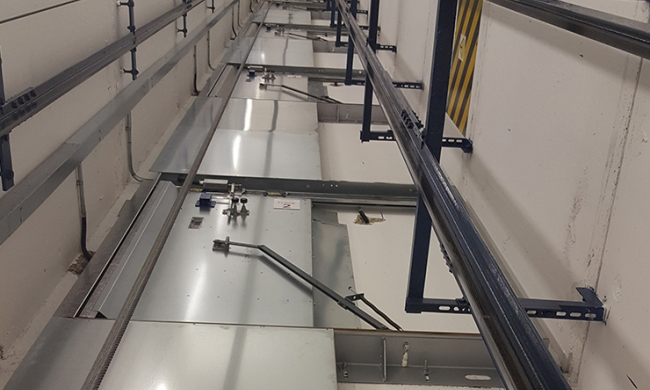
Additional Services:
- Report for estimated life expectancy for lift and mobility equipment.
- Budget forecasting for future spending plans.
- Record and monitor lift LOLER inspections and advise on remedial actions.
- Quality control inspections on mobility equipment.
- Monitoring of the contractor's performance and competence.
- Management of the service and maintenance contract.
- Construction design & management client advisory.
- Practical completion client handover.
- Expert witness testing on commissioning of refurbishment and new installations.
- Inspection of site specific completed operation and maintenance manual.
How Can We Help
Our specialist lift consultants provide expert advice and independent consultancy on a comprehensive range of passenger lift and mobility equipment repair and maintenance, management system audits, stock condition surveys and project management to assist you in complying with the statutory requirements.
Visit our contact page for more information or fill out the contact form at the bottom of this page and we will get back to you as soon as we can.
Do you have an obligation to maintain your lift equipment?
The lift equipment will require maintenance in line with two pieces of legislation, PUWER (The Provision and Use of Work Equipment Regulations) and LOLER (The Lifting Operations and Lifting Equipment Regulations). The lift is considered an item of work equipment and that places a legal obligation on the lift owner to take all necessary steps to ensure the lift is safe for the use of its residents, employees and the public.
Who can provide a Lifting Operations and Lifting Equipment Regulations 1998 (LOLER) certificate?
The lift equipment should have a LOLER inspection carried out by a competent person. LOLER Approved Code of Practice and guidance (paragraph 294 on competent persons) states that: 'You should ensure that the person carrying out a thorough examination has such appropriate practical and theoretical knowledge and experience of the lifting equipment to be thoroughly examined as will enable them to detect defects or weaknesses and to assess their importance in relation to the safety and continued use of the lifting equipment.'
How often should thorough examinations be carried out?
In order to verify that lifting equipment and accessories remain safe for use, and to detect and remedy any deterioration in good time, thorough examinations are required throughout the lifetime of the equipment, including examinations:
- before use for the first time - unless the equipment has an EC Declaration of Conformity less than one year old and the equipment was not assembled on site. If it was assembled on site, it must be examined by a competent person to ensure that the assembly (e.g a platform lift installed in a building) was completed correctly and safely after assembly and before use at each location - for equipment that requires assembly or installation before use, e.g tower cranes.
- regularly, while in service - if the equipment is exposed to conditions that cause deterioration which is likely to result in dangerous situations. Most lifting equipment will be subject to wear and tear and so will need regular in-service examination. Some may be exposed to significant environmental conditions which may cause further deterioration. You have a choice to:
- arrange for thorough examination to be carried out at the intervals specified by LOLER (every 6 or 12 months, depending on the equipment - see below), or
- conduct examinations in accordance with an examination scheme, drawn up by a competent person.
Source: www.hse.gov.uk
How often should your lift be maintained?
The frequency of service visits depends on the manufacturer's instructions, frequency of use, the number of floors served and the building occupancy. Lift servicing is about improving the longevity of your lift and having your lift regularly serviced is likely to minimise your running costs in the medium to long term, making it a cost effective way of ensuring your lift maintains its efficiency, reliability and safety.
What type of service contract is appropriate for you?
A basic contract is where everything other than service visits are chargeable and a fully comprehensive includes breakdowns and repairs, as well as the cost of replacement parts and labour. The contractor will produce a dilapidation report for each lift upon their initial service visit which will indicate where certain major parts or components are to be removed from the contract due to age, wear and tear or obsolescence. A comprehensive contract will normally not include working upon arrival callouts, misuse/vandalism and obsolescent parts.